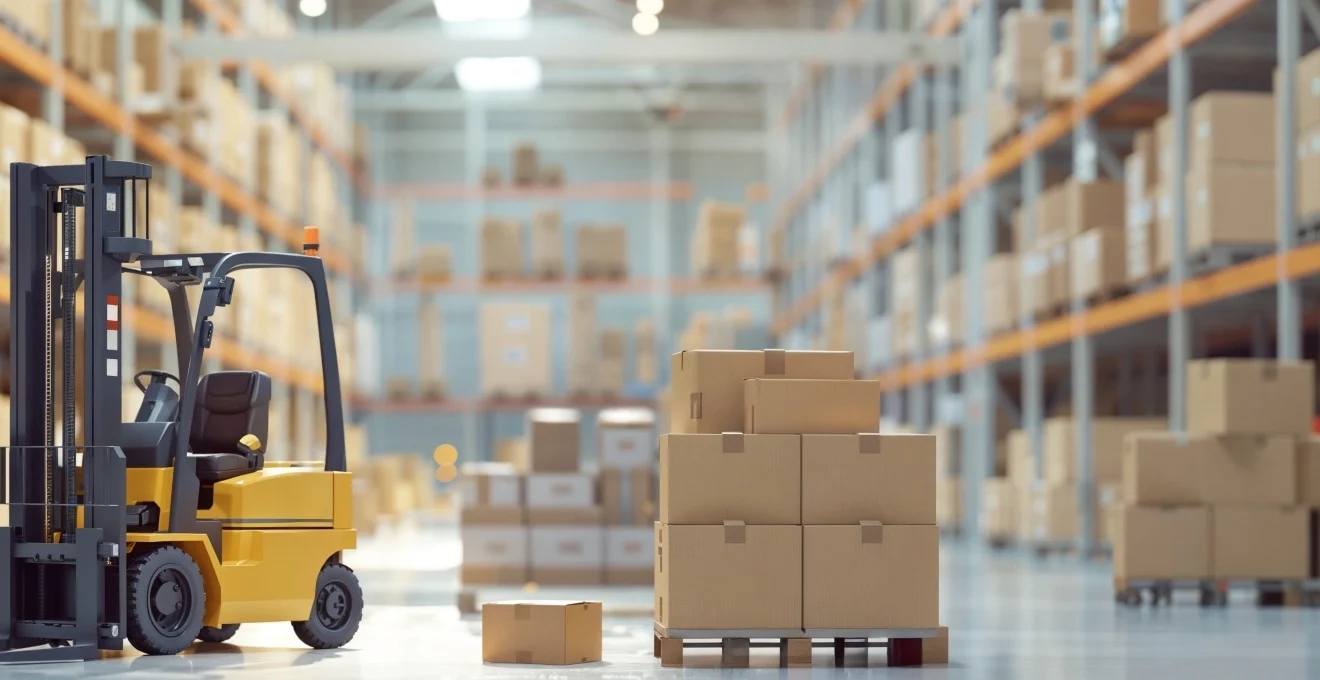
La gestion efficace du stockage industriel est un enjeu majeur pour les entreprises cherchant à optimiser leurs coûts opérationnels. Dans un contexte économique où chaque euro compte, repenser sa stratégie de stockage peut s'avérer être un levier puissant pour réduire les dépenses tout en améliorant la productivité. Que vous soyez une PME ou un grand groupe industriel, les solutions innovantes en matière de stockage industriel offrent de nombreuses opportunités d'économies.
Analyse des coûts de stockage industriel
Avant de mettre en place une stratégie d'optimisation, il est important de comprendre en détail la structure de vos coûts de stockage. Ces derniers se décomposent généralement en plusieurs catégories : les coûts immobiliers (location ou amortissement des bâtiments), les coûts d'équipement (rayonnages, chariots élévateurs), les coûts de main-d'œuvre, les coûts énergétiques, et les coûts liés à la gestion des stocks (obsolescence, détérioration).
Une analyse approfondie révèle souvent des zones d'inefficacité insoupçonnées. De plus, les coûts liés à une mauvaise gestion des stocks peuvent représenter jusqu'à 20% du coût total de stockage pour certaines entreprises.
Pour réaliser cette analyse, vous pouvez utiliser des outils de business intelligence spécialisés dans la logistique. Ces solutions permettent de visualiser clairement la répartition de vos coûts et d'identifier les postes les plus gourmands. Une fois cette cartographie établie, vous serez en mesure de cibler vos efforts d'optimisation sur les aspects les plus impactants.
Optimisation de l'espace de stockage
L'optimisation de l'espace est souvent le premier levier actionné pour réduire les coûts de stockage. En effet, maximiser l'utilisation de chaque mètre carré permet non seulement de réduire les coûts immobiliers, mais aussi d'améliorer l'efficacité opérationnelle. Voici quelques stratégies éprouvées pour y parvenir :
Systèmes de rayonnage à haute densité
Les systèmes de rayonnage à haute densité sont conçus pour maximiser l'utilisation de l'espace vertical et horizontal. Contrairement aux rayonnages traditionnels, ces systèmes permettent de stocker plus de produits dans un espace donné.
Utilisation de mezanines et plateformes
L'installation de mezanines ou de plateformes intermédiaires est une excellente façon d'exploiter la hauteur de vos entrepôts. Cette solution permet de créer un nouvel espace de stockage sans augmenter la surface au sol. Selon une étude récente, l'ajout d'une mezanine peut accroître la capacité de stockage de 30 à 60%, en fonction de la configuration de l'entrepôt.
Stockage vertical avec transtockeurs
Les transtockeurs sont des systèmes automatisés de stockage vertical qui peuvent atteindre des hauteurs impressionnantes, parfois jusqu'à 40 mètres. Ces équipements sont particulièrement efficaces pour les entreprises gérant un grand nombre de références avec des mouvements fréquents. Ils permettent non seulement d'optimiser l'espace, mais aussi de réduire considérablement les temps de picking.
Optimisation des allées avec chariots à mât rétractable
L'utilisation de chariots élévateurs à mât rétractable permet de réduire la largeur des allées de circulation dans votre entrepôt. Ces engins peuvent opérer dans des allées de seulement 2,5 mètres de large, contre 3,5 à 4 mètres pour des chariots conventionnels. Cette réduction peut libérer jusqu'à 25% d'espace supplémentaire pour le stockage.
L'optimisation de l'espace de stockage n'est pas une simple question de gain de place, c'est une stratégie globale qui impacte directement la productivité et la rentabilité de l'entreprise.
Automatisation des processus de stockage
L'automatisation est un levier puissant pour réduire les coûts de stockage tout en améliorant la précision et la rapidité des opérations. Bien que l'investissement initial puisse être conséquent, le retour sur investissement est souvent rapide, notamment pour les entreprises gérant de gros volumes.
Systèmes de gestion d'entrepôt (WMS) performants
Un Warehouse Management System (WMS) moderne est le cerveau de votre entrepôt. Il optimise l'utilisation de l'espace, gère les flux de produits et pilote les opérations de picking. Les dernières générations de WMS intègrent des algorithmes d'intelligence artificielle pour prédire les besoins et optimiser en temps réel le placement des produits.
Robotisation avec AGV et AMR
Les AGV
(Automated Guided Vehicles) et les AMR
(Autonomous Mobile Robots) révolutionnent la manutention dans les entrepôts. Ces robots peuvent effectuer des tâches de transport, de picking et même de tri, 24h/24 et 7j/7. Ils réduisent non seulement les coûts de main-d'œuvre, mais aussi les erreurs et les accidents de travail. Selon une analyse récente, l'utilisation d'AGV peut diminuer les coûts de manutention de 20 à 40% dans certains contextes.
Convoyeurs automatisés et trieurs
Les systèmes de convoyage automatisés et les trieurs haute performance sont essentiels pour les entreprises gérant un grand nombre de commandes. Ils accélèrent considérablement le processus de préparation et de distribution des commandes, réduisant ainsi les temps de cycle et les coûts associés.
Technologies RFID pour le suivi des stocks
La technologie RFID (Radio Frequency Identification) permet un suivi précis et en temps réel des stocks. Elle réduit les erreurs d'inventaire, améliore la traçabilité et facilite la gestion des rotations. Bien que le coût d'implémentation puisse sembler élevé, le ROI est généralement atteint en 12 à 18 mois grâce à la réduction des pertes et à l'optimisation des niveaux de stock.
Stratégies de gestion des stocks avancées
Une gestion fine des stocks est importante pour minimiser les coûts de stockage tout en assurant un niveau de service optimal. Voici quelques stratégies avancées qui ont fait leurs preuves :
Méthode ABC pour la classification des produits
La méthode ABC consiste à classer les produits en trois catégories selon leur importance en termes de chiffre d'affaires ou de fréquence de picking. Cette approche permet d'optimiser le placement des produits dans l'entrepôt et d'ajuster les niveaux de stock en conséquence.
Techniques de réapprovisionnement kanban
Le système Kanban, initialement développé par Toyota, est une méthode de gestion des flux tendue qui vise à minimiser les stocks tout en évitant les ruptures. Il repose sur des signaux visuels ou électroniques pour déclencher le réapprovisionnement juste à temps. Cette approche peut réduire les niveaux de stock de 20 à 50% tout en améliorant le taux de service.
Prévision de la demande par intelligence artificielle
Les algorithmes d'IA modernes sont capables d'analyser de grandes quantités de données pour prédire la demande future avec une précision remarquable. Ces outils prennent en compte non seulement l'historique des ventes, mais aussi des facteurs externes comme la météo, les tendances des réseaux sociaux ou les événements économiques. Une prévision précise permet d'ajuster finement les niveaux de stock, réduisant ainsi les coûts de stockage et le risque d'obsolescence.
Optimisation des niveaux de stock avec le just-in-time
Le principe du Just-in-Time (JIT) vise à réduire au maximum les stocks en synchronisant parfaitement les approvisionnements avec la demande. Bien que difficile à mettre en œuvre, cette approche peut conduire à des réductions drastiques des coûts de stockage.
La gestion avancée des stocks n'est pas seulement une question de réduction des coûts, c'est aussi un moyen d'améliorer la réactivité et la compétitivité de l'entreprise sur son marché.
Rationalisation de la manutention
La manutention représente souvent une part importante des coûts opérationnels d'un entrepôt. Rationaliser ces opérations peut donc avoir un impact significatif sur vos coûts globaux de stockage. Voici quelques approches efficaces :
Tout d'abord, l'optimisation des parcours de picking est importante. L'utilisation d'algorithmes avancés peut réduire considérablement les distances parcourues par les opérateurs.
Ensuite, la mise en place d'un système de batch picking ou de zone picking peut augmenter significativement la productivité. Le batch picking consiste à regrouper plusieurs commandes pour les préparer simultanément, tandis que le zone picking divise l'entrepôt en zones spécifiques, chaque opérateur étant responsable d'une zone.
L'utilisation de technologies d'assistance comme les systèmes de picking vocal ou les lunettes de réalité augmentée peut également améliorer l'efficacité et la précision des opérations de manutention. Ces technologies permettent aux opérateurs de travailler en mains libres, accélérant ainsi les processus tout en réduisant les erreurs.
Enfin, la formation continue des opérateurs aux meilleures pratiques de manutention est essentielle. Des opérateurs bien formés sont non seulement plus efficaces, mais ils contribuent aussi à réduire les dommages aux produits et les accidents de travail, deux sources importantes de coûts cachés.
Externalisation stratégique du stockage
L'externalisation du stockage peut être une option intéressante pour réduire les coûts, en particulier pour les entreprises confrontées à des fluctuations saisonnières importantes ou à des contraintes d'espace. Cependant, cette décision doit être prise de manière stratégique et réfléchie.
Les avantages de l'externalisation incluent la transformation de coûts fixes (entrepôts, équipements) en coûts variables, une plus grande flexibilité pour s'adapter aux variations de volume, et l'accès à des expertises et technologies spécialisées.
Cependant, l'externalisation comporte aussi des risques, notamment en termes de contrôle des opérations et de qualité de service. Il est important de choisir un partenaire logistique fiable et de mettre en place des indicateurs de performance (KPI) précis pour suivre l'efficacité de la collaboration.
Une approche hybride, combinant stockage interne pour les produits à forte rotation et externalisation pour les produits saisonniers ou à faible rotation, peut offrir un bon équilibre entre contrôle des coûts et flexibilité opérationnelle.